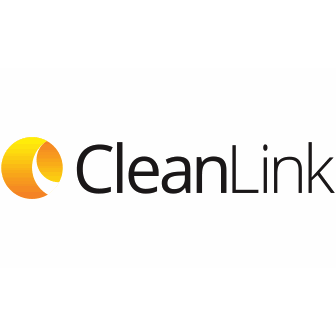
Product labels, data sheets, and safety data sheets should contain everything managers need to know to educate workers on the proper use of chemicals. This determines the effectiveness of the chemicals.
"You have to play by the rules," adds Fellows.
This also includes paying attention to dwell times. Depending on the label, most disinfectants need to remain on a surface for 30 seconds to 10 minutes to disinfect the pathogens listed. Caregivers often don't wait that long to clean, which means the sanitizer isn't effective.
"Tracking dwell times (aka wet times or contact times) is critical because when workers don't do this, they can contribute to the development of superbugs," says Sawchuk. "If the label recommends a contact time of 10 minutes and you wait just eight minutes, the weaker pathogens are likely dead. But those that survive will produce superbugs that can survive disinfection."
Cleaners who know the exposure time can spray any surface with disinfectant and then wait the required time before cleaning. Depending on the technology, that could also be a mistake, adds Fellows.
"When we use spray bottles to apply the disinfectant, 40-60% of the surface stays dry - the disinfectant never touches it," he says.
Hicks calls this method sprinkle and pray.
"The proper way to disinfect is to take a microfiber cloth folded in four, dampen the cloth with disinfectant, and then wet the surface enough to stay wet for the recommended exposure time," he says. .
Hicks also recommends regularly checking the dilution control systems to ensure proper chemical dilution. Let's say a quaternary disinfectant is effective at 600 parts per million. If no one checks the system, workers could get 300 parts per million instead. In this case, weakened disinfectants are used on surfaces and destruction claims are not met.
"The microorganisms then learn to resist that disinfectant, and you can't kill them," notes Hicks.
Prioritize training
There's a lot to consider, so Fellows recommends that managers start writing Standard Operating Procedures (SOPs) that clearly describe products, processes, and frequencies for chemical use. This is followed by demonstrations of the writing process. Later, supervisors can check in to ensure guards are following SOPs.
"Every janitor should also have a copy of the steps," says Fellows. "People can't remember everything, especially when it's a new process."
He also recommends checking shifts regularly and observing workers as they carry out their tasks. This is a great opportunity to provide training immediately if steps are missed.
"It takes 90 days to form a habit," says Fellows. "Old habits will set in if you don't systematically reinforce these new skills."
When management can't see live the work being done, Hicks suggests two common monitoring practices: Managers can mark surfaces with a fluorescent marker before cleaning and then use a black light to see if the cleaning has removed the soiling, or they can use it an ATP meter to measure the level of contamination before and after cleaning.
"We need to go back to basics and deep clean, and then measure our processes, our products, and our people," says Hicks.
But he insists that observation must also be part of the puzzle.
"If you're not watching how they do things, you're measuring the results and you don't know why they failed inspection, where the cleaning went wrong and what's broken," he says. "Maybe they don't have the right products or tools for the job. Maybe they don't have the time to get it right. Or maybe they need more training."
Chemicals have received a lot of attention in recent years, but it's time to get back to basics. Select the right products for the job, develop an SOP, provide training, and follow a quality control initiative to measure results. Make adjustments as needed to ensure the team is properly using products to clean, sanitize, and disinfect surfaces.
Ronnie Wendt is a freelance writer and owner of In Good Company Communications based in Waukesha, Wisconsin.
PUBLISHED ON: 02/16/2022
Aucun commentaire:
Enregistrer un commentaire